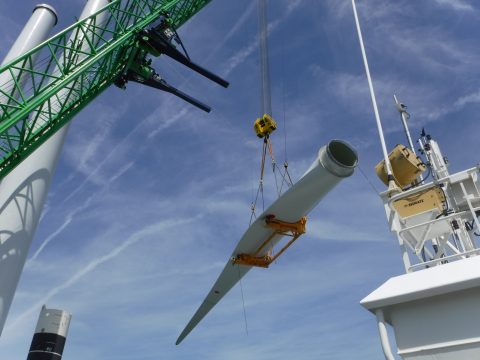
As demands on offshore wind installation processes increase, crane technology is being pushed to its limits. Not only do offshore cranes need to lift heavier and larger wind turbine components, but they also need to operate in more gruelling weather conditions.
Increasingly, vessel owners and contractors are looking to meet these demands by boosting crane capabilities with technologies such as taglines and various forms of intelligent lifting systems. But there are important implications of these additional demands that impact crane design and performance.