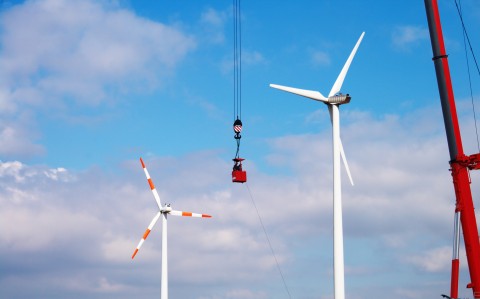
As offshore wind turbine sizes grow rapidly, the technology needed to install and commission turbines is not following suit. This is a significant barrier to progress in the offshore wind industry and is continuing to make it difficult to reduce the levelised cost of energy.
Today’s wind turbines and the associated installation technology, such as taglines, have been created from the same baseline. But it is all essential just an incremental evolution of technologies that have been moved from onshore to offshore. There have been no significant design revolutions.
At the same time, we are using the same technology developed for smaller turbines and assuming it will deal with 8MW turbines – and bigger. We are increasingly demanding more from the equipment, but in reality the technology has its limits.
Manual intervention
Turbine installation currently requires considerable individual expertise and experience as well as frequent manual physical intervention. For example, instead of people needing to handle the guiding ropes, automation technology could help the process to be much more controlled.
The cranes themselves are also a limiting factor. As long as we use classic cranes fitted with specific lifting tools, such as simple tagline systems, it will always be near impossible to maintain full control over the lifting operations, no matter what you do to compensate for factors such as weather conditions and installation speed.
And a lack of control will often lead to delays, which increases costs. The industry target of 100 EUR/MW seems even more distant.
With the new generation of turbines, we will soon see that legacy methods are no longer good enough. Particularly as project owners demand shorter project times and improved safety conditions, new methods will have to be adopted.
Technology demarcation
A key barrier for adopting new solutions is found in the industry structure. The demarcation of the industry is based on the main industry players: vessel owners, turbine manufacturers and wind farm developers. Not only are contracts structured according to this demarcation, but it has also driven a technology demarcation.
Across the industry, significant technological developments are following closely on the heels of increasing size of turbines. Crane booms are being extended. Jack-ups are being purpose-built to handle harsher weather conditions. The larger turbine manufacturers are developing installation tools specifically for their turbine components.
But the missing link seems to be the compatibility with the installation vessel. Turbine manufacturers and, indeed, the industry as a whole expect that any jack-up can be used for installation and that the installation tools are compatible with all cranes.
For the industry to make a significant breakthrough in efficiencies, particularly when it comes to turbine installation in higher winds, installation vessel design will need to take the next step. Currently, vessels need to be able to handle heavy foundation lifts, which are not that wind sensitive, while also managing turbine component lifts, which are very wind sensitive. With this versatility, there is a danger the industry will neglect valuable technology innovations, such as specialised crane design and vessels designed specifically for installing wind turbines.
Purpose-built cranes
With the increasing tendency of vessel owners to take on EPCI contracts, the installation operation is becoming their responsibility and liability. This is one key reason vessel owners need to look at specific equipment, with the crane being an obvious place to start.
Giving the crane more advanced functionality, for example, will improve installation efficiency, speed and safety, ensuring lifting operations are guided and controlled from deck to turbine, with absolutely no manual intervention required. Adverse environmental conditions, such as sudden wind gust or sudden movement (mistake), would be mitigated or avoided altogether.
If we look ahead five years, I believe we can eliminate the need for people to pull ropes or guide blades as they fight the wind. The norm will be that installation is completely mechanically guided, either by structures or by taglines. Being able to fully control installation without the risk of human error and or the limitations of environmental conditions is the way forward.
It will require further adoption of new technologies and a few changes to industry structures, too. But with lower costs, decreased risk of damage, and better safety, it will surely be worth it.
Like this post? Subscribe now and get notified about new content!